双光束激光焊接
Jul 11,2025
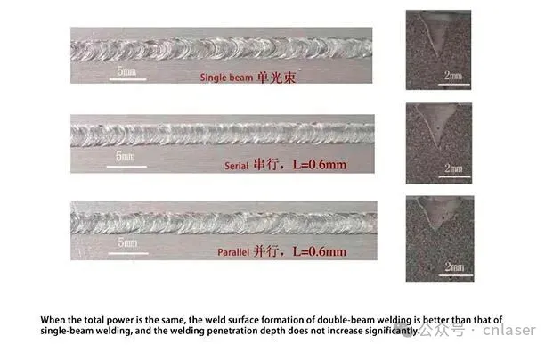
本文讨论了双光束焊接方法,主要用于提高激光焊接对装配精度的适应性,增加焊接过程的稳定性,提高焊缝质量,特别适用于薄板、铝合金等材料的焊接。双光束焊接方法的提出,主要是为了提高激光焊接对装配精度的适应性,增加焊接过程的稳定性,提高焊缝质量,尤其适用于薄板及铝合金的焊接。双光束激光焊接既可以将同一种类型的激光器利用光学方法分成两束独立的激光进行焊接,也可以采用两种不同类型的激光器进行组合焊接。CO2激光器、Nd:YAG激光器、大功率半导体激光器等都可以相互组合。通过改变光束的能量、光束间的距离,甚至两束激光的能量分布模式,可以方便灵活地调节焊接温度场,从而改变孔洞的存在方式和熔池中液态金属的流动方式,为焊接工艺提供了更为广泛的选择空间,这是单光束激光焊接无法比拟的。它不仅具备激光焊接熔深、速度快、精度高等优势,而且对常规激光焊接难以焊接的材料和接头具有很强的适应性。
1.双光束激光焊接原理
双光束焊接是指在焊接过程中同时使用两束激光器。光束排列、光束间距、两束光束所形成的夹角、聚焦位置以及两束光束的能量配比都是双光束激光焊接中相关的设置参数。通常,在焊接过程中,双光束的排列方式通常有两种。如图所示,一种是沿焊接方向串联排列,这种排列方式可以降低熔池的冷却速度,减少焊缝的硬化趋势和气孔的产生。另一种是将光束并排或交叉排列在焊缝两侧,以增加对焊缝间隙的适应性。
对于串联布置的双光束激光焊接系统,根据两光束之间的间距,有三种不同的焊接机制。
1)第一种焊接机理中,两束光束间距较大,一束能量密度较高,聚焦于工件表面,焊接时产生小孔;另一束能量密度较低,仅作为焊前或焊后热处理的热源。这种焊接机理使得焊接熔池的冷却速度可以控制在一定范围内,有利于高碳钢、合金钢等裂纹敏感性材料的焊接,同时也能提高焊缝的韧性。
2)在第二种焊接机理中,两束激光焦点之间的距离相对较小。两束激光在单个熔池中产生两个独立的小孔,从而改变熔融金属的流动模式。这有助于防止咬边、焊道突出等缺陷,改善焊缝成形。
3)第三种焊接机理中,两束激光之间的间距很小,此时两束激光在焊接熔池中产生相同的匙孔。相比单束激光焊,这个匙孔尺寸更大,且不易闭合,使焊接过程更加稳定,气体更容易排出。这有利于减少气孔、飞溅,获得连续、均匀、美观的焊缝。
焊接过程中,两束激光也可设置成一定的角度,其焊接机理与平行双光束焊接机理类似。试验结果表明,采用两束高功率OO激光以30°夹角、间距1~2mm的条件组合,可获得漏斗状的匙孔,匙孔更大、更稳定,可有效提高焊接质量。实际应用中,可根据不同的焊接情况调整两束激光的不同组合,以实现不同的焊接工艺。
2.双光束激光焊接的实现方法
通过将两束不同的激光合束,或者使用光学分束系统将一束激光分成两束用于焊接,可以实现双光束输出。要将一束激光分成两束不同的功率,可以使用平行激光器、分束镜或一些特殊的光学系统。图中展示了两种使用聚焦透镜作为分束器的分束原理。
另外,反射镜可以用作分束镜,光路中最后一个反射镜作为分束器。这种反射镜又称脊形反射镜,它的反射面不是单一平面,而是由两个平面构成,两个反射面的交线位于镜面的中间,形似一条脊线,如图所示。一束平行光束投射到分束镜上,被两个不同角度的平面反射成两束光束,照射到聚焦透镜上的不同位置,聚焦后在工件表面得到两束具有一定间距的光束。通过改变两个反射面之间的夹角和脊线的位置,可以得到不同焦距和排布方式的分束光束。
采用两种不同类型的激光束组成双光束时,有多种组合方式。可以采用高斯能量分布的高质量CO2激光器进行主焊接工作,辅以矩形能量分布的半导体激光器进行热处理工作。这种组合方式一方面经济实惠,另一方面两束激光的功率可以独立调节。针对不同的接头形式,通过调节激光器和半导体激光器的重叠位置可以获得可调的温度场,非常适合焊接过程控制。此外,还可以将YAG激光器与CO2激光器组合成双光束进行焊接,将连续激光与脉冲激光组合进行焊接,还可以将聚焦光束与散焦光束组合进行焊接。
3.双光束激光焊接原理
3.1镀锌板双光束激光焊接
镀锌钢板是汽车工业中最常用的材料。钢的熔点在1500℃左右,而锌的沸点只有906℃。因此,采用焊接方法时,通常会产生大量的锌蒸气,导致焊接过程不稳定,并在焊缝中形成气孔。对于搭接接头,镀锌层的挥发不仅发生在上下表面,也发生在接头界面处。焊接过程中,有些区域锌蒸气迅速喷出熔池表面,而有些区域锌蒸气难以逸出熔池表面,导致焊接质量极不稳定。
双光束激光焊接可以解决锌蒸气引起的焊接质量问题。一种方法是通过合理匹配两束激光的能量来控制熔池的停留时间和冷却速度,有利于锌蒸气的逸出;另一种方法是通过预钻孔或开槽处理,使锌蒸气得以逸出。如下图所示,采用CO2激光器进行焊接,在CO2激光器正面的YAG激光器用于钻孔或开槽。预加工的孔或槽为后续焊接产生的锌蒸气提供了逸出通道,避免其滞留在熔池中形成缺陷。
3.2 铝合金双光束激光焊接
由于铝合金材料的独特性能,激光焊接存在以下难点:铝合金对激光的吸收率较低,CO2激光束表面初始反射率超过90%;焊接过程中铝合金激光焊缝易产生气孔和裂纹;焊接过程中存在合金元素的损失。单光束激光焊接时,匙孔形成困难,且不易维持稳定。采用双光束激光焊接时,可以增大匙孔尺寸,使匙孔不易闭合,利于气体排出。同时,可以降低冷却速度,减少气孔和焊接裂纹的产生。由于焊接过程更加稳定,飞溅量减少,铝合金双光束焊接获得的焊缝表面成形也明显优于单光束。下图为单光束CO2激光束和双光束激光束焊接3mm厚铝合金对接接头的形貌。
研究表明,焊接2mm厚5000系列铝合金时,当两光束间距为0.6~1.0mm时,焊接过程相对稳定,形成的匙孔开口较大,有利于焊接过程中镁元素的蒸发和逸出。两光束间距过小,焊接过程类似单光束焊接,不易稳定;间距过大,则会影响焊接熔深,如下图所示。此外,两光束的能量比对焊接质量也有显著影响。当两光束以0.9mm间距串联焊接时,适当增加前一光束的能量,使两光束能量比大于1:1是有利的,这有助于提高焊缝质量,增大熔化面积,即使在较高的焊接速度下,也能获得光滑美观的焊缝。
3.3 不等厚板双光束焊接
在工业生产中,经常需要将两块或多块不同厚度、不同形状的金属板材焊接在一起,形成拼合板。尤其是在汽车制造中,拼合板的应用越来越广泛。
通过将不同规格、表面镀层或性能的板材焊接在一起,可以提高强度、降低能耗、减轻重量。在拼合板焊接中,通常采用不同厚度板材的激光焊接。其主要问题是需要预先加工出边缘精度高的待焊工件,并确保高精度的装配。对于不等厚板材,采用双光束焊接可以适应板材间隙、对接部位、相对厚度和材质的不同,可以焊接边缘和间隙公差较大的板材,提高焊接速度和焊缝质量。
不等厚板材双光束焊接的主要工艺参数可分为焊接参数和板材参数,如图所示。焊接参数包括两束激光器的功率、焊接速度、焦点位置、焊头角度、双光束在对接接头处的光束旋转角度以及焊接偏差。板材参数包括材料尺寸、性能、边缘修整和板材间隙。两束激光器的功率可根据不同的焊接目的分别调整。
通常,当焦点位于薄板表面时,焊接过程稳定高效。焊头角度通常选择在6度左右。如果两块板材的厚度较大,可以采用正焊头角度,即激光如图所示向薄板倾斜。当板材厚度较小时,可以采用负焊头角度。焊接偏差定义为激光焦点与厚板边缘之间的距离。通过调整焊接偏差,可以减小焊缝凹陷,从而获得良好的焊缝截面。
焊接间隙较大的板材时,可以通过旋转双光束角度来增大有效光束加热直径,以达到良好的间隙填充能力。焊缝顶部的宽度由两束激光器的有效光束直径决定,也就是由光束旋转角度决定。旋转角度越大,双光束加热范围越宽,焊缝顶部宽度也越宽。两束激光器在焊接过程中起着不同的作用,一束主要用于熔透接头,另一束主要用于熔化厚板材料以填充间隙。如下图所示,在正光束旋转角度下(前光束作用于厚板,后光束作用于焊缝),前光束撞击厚板,加热熔化材料,后续激光束产生穿透。最前方的第一束激光只能部分熔化厚板,但它对焊接过程的贡献很大,因为它不仅熔化了厚板侧面以更好地填充间隙,而且还预连接了接头材料,使后续光束更容易穿透接头,从而提高了焊接速度。在负旋转角度(前光束作用于焊缝,后光束作用于厚板)的双光束焊接中,两束激光的作用正好相反,前光束穿透接头,后光束熔化厚板并填充间隙。
此时,前束激光需要穿透冷板,焊接速度比正光束旋转角度时要低。同时,由于前束激光的预热作用,相同功率下后束激光会熔化更多的厚板材料。此时应适当降低第二束激光的功率。相较而言,采用正光束旋转角度可以适当提高焊接速度,而采用负光束旋转角度则可以获得更好的间隙填充效果。下图展示了不同光束旋转角度对焊缝横截面的影响。
3.4 厚板双光束激光焊接
随着激光功率水平和光束质量的提高,厚板激光焊接已成为现实。然而,由于高功率激光器成本较高,且厚板焊接普遍需要金属填充,在实际生产中受到一定的限制。采用双光束激光焊接技术,不仅提高了激光功率,而且增加了光束有效加热直径,增强了填充焊丝的熔化能力,并稳定了激光小孔,提高了焊接稳定性,从而提高了焊接质量。
*本资料部分信息源于公开网络渠道,其版权归属原作者所有。
若内容涉及版权争议或授权问题,请通过halllaser@halllaser.com 联系我司,我们将依法配合处理。
上一页:
下一页: